Chapter 20 Materials and Material Properties
The first recorded use of a metallic implant device was in 1804, when a steel implant was used in a fracture repair.1,2 Later, in 1924, stainless steel, which contains 18% chromium and 8% nickel, was first applied for medical purposes. The next major advance in metallurgy was the aircraft industry’s development of light-weight but resilient metals known as titanium alloys.1,2 In the 1950s, the biomedical field began to make use of titanium. Currently, titanium is one of the most advantageous metals for implant use because of its high strength, low modulus, and high corrosion resistance.1
Forces
The International System (SI units), which is based on the metric system, is the nomenclature used by the biomedical engineering profession. The newton (N) is a direct measure of force and is recorded as intrinsic units: kg(m)/sec2. As defined by Newton’s second law, force is equivalent to the product of mass and acceleration. Forces, when applied to the spine, not only consist of a magnitude but also have a directional component. The combination of a force with direction is a vector. Vectors can be displayed graphically or by trigonometric relationships. Vectors can be used to analyze biomechanical forces acting simultaneously on a biologic structure or implant material by making a free body diagram that assumes a state of equilibrium, thereby defining the forces inside the structure or implant material as dependent and proportional to those outside the structure (Fig. 20-1).
A very important principle for the spine surgeon to understand is the force-deformation relationship (Fig. 20-2). When force and deformation are graphically displayed, the result is a characteristic curve. The force-deformation curve has a straight or elastic region in which materials can deform and recover to their original shape (see Fig. 20-2, first portion of curve). As the load increases beyond the elastic region, the deformation increases into the curved or plastic region (see Fig. 20-2, second portion of curve); when the specimen is unloaded, it will be permanently deformed. If deformation is continued, the specimen will eventually fail (e.g., fracture; see Fig. 20-2, third portion of curve).
The integrity of the spine is multifactorial. The vertebral body ossifies from three primary centers, one for the centrum, which will form the major portion of the body, and the other two for neural arches. The cartilaginous growth plate is mainly responsible for longitudinal vertebral growth. The vertebral body design, therefore, provides the requirement for optimal load transfer by maximal strength with minimal weight. Bone mineral density (BMD), bone quality, microarchitecture, and material properties are the important factors that contribute to bone strength.3 In addition, force and displacement have been demonstrated in animal spine models. It has been demonstrated in a biomechanical cadaver study that after dorsal laminectomy and partial discectomy, the neutral zone and range of motion were not different from those in the native spine specimen. However, after pedicle screw-rod fixation, the neutral zone and range of motion of the instrumented specimen decreased significantly compared with the native specimen and the specimen after dorsal laminectomy.4
Atomic Bonds, Structures, and Property Relationships
Metals are created through the interaction of crystals. These crystals are formed when the electrons that surround the atoms in clouds are given up and conducted as electricity. Metal structures are polycrystalline (i.e., they are formed by a multitude of crystals). Atoms within a crystal can form one of several relationships, which define the crystal structure. They include body-centered cubic, face-centered cubic, and hexagonal close-packed arrangements (Figs. 20-3 to 20-5).
Point defects occur when a lattice site within a crystal is empty and not occupied by an atom.1,5 Point defects are present in all metals and provide a mechanism for diffusion, which is the movement of solute through a solvent.
Line defects are microscopic dislocations and are the major defect affecting a given metals mechanical properties. Line defects occur when there is an incomplete chain of atoms inside a crystal. This results in a local distortion of the structure of the crystal because of the resultant dislocation. There is considerable internal strain in the immediate vicinity of the dislocation. When a force is applied, the line defect can propagate through the crystal structure, resulting in a permanent structural change (Figs. 20-6 and 20-7). This is termed plastic deformation. When a metal is plastically deformed, a permanent structural change persists after the force is removed from the metal.1
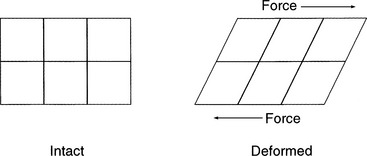
FIGURE 20-7 Deformation occurs when parallel and opposite forces are applied to a structure with one side immobilized.
An example of an area defect is a grain boundary.1 When metal begins the solidification process, crystals form independently of one another. Each crystal grows into a crystalline structure, or grain. The size and number of grains developed by a certain amount of metal depend on the rate of nucleation, which is the initial stage of formation of a crystal. Rapid cooling usually produces smaller grains, whereas slower cooling produces larger grains. The orientation of crystal boundaries (grain boundaries) is very influential in the spread of dislocations that become cracks.
Mechanical Properties
Knowing the dimensions of a material, when a force is applied, permits the stress or load per unit area to be determined. Stress is recorded as N/m2 (Pascal) and is a small quantity. Therefore, most materials are tested with thousands of N/m2, or megapascals. Strain is a dimensionless unit that is the percentage of elongation (or shortening) during application of force. When both the load and the deformation are divided by the original area or length of the specimen, respectively, the result is stress and strain, which can be displayed graphically (see Fig. 20-7).
Spine surgeons should have a basic understanding of the typical stress-strain curve (see Fig. 20-2). The stress-strain curve defines the mechanical behavior of a metal under various degrees of stress and strain. The ratio of stress to strain is the modulus, or elastic modulus. The relationship is as follows:
Spinal Implants: Rigid versus Dynamic
The widespread use of instrumentation in the lumbar spine has led to high rates of fusion. This has been accompanied by a marked rise in adjacent-segment disease, which is considered to be an increasingly common and significant consequence of lumbar or lumbosacral fusion. Numerous biomechanical studies have demonstrated that segments fused with rigid metallic fixation lead to significant amounts of supraphysiologic stress on adjacent discs and facets. Although this form of arthrodesis does not completely prevent adjacent-segment disease, the dynamic component of this stabilization technique may minimize its occurrence.6 Posterior dynamic stabilization (PDS) devices have shown a substantial reduction in stress-shielding characteristics. Higher axial load was noted with the PDS devices, which could slow the degeneration process of bony structures and lower the possibility of implant failure.7
Biologic Materials
The stiffness of bone is approximately 10% that of stainless steel and 20% that of titanium alloy (Ti-6Al4V, or simply 116-4). This means that the stiffness of bone is closer to that of titanium than steel implants. This fact has been used to suggest that there is a better “match” between titanium and bone than between stainless steel and bone. In certain circumstances this might be important, such as when a permanently implanted device will be subjected to repeated deformations while the bone-implant juncture could loosen. Alternatively, the use of steel implants creates a construct of higher stiffness. Surgical constructs of higher stiffness have been associated with higher fusion rates, both clinically and experimentally. Because the optimal stiffness of a surgical construct for bone healing is unknown, the selection of implant material should not be influenced by minor variations in the stiffness of materials.
Stainless Steel
Initial trials of stainless steel as an implant showed that resisting corrosion by improving resistance to chloride degradation was insufficient. The addition of molybdenum and chromium reduced the incidence of corrosion and pitting by aiding the defense against chloride degradation.1,5
The 316 stainless steels, which have a face-centered cubic structure, are the steels that are used most commonly for spinal implants. There are two grades, grade 1 (316) and grade 2 (316L), of which grade 2 has the lower carbon content. The lower carbon content aids in reducing the formation of metal carbides, which leads to a decrease in the corrosion resistance of the alloy.1,8 These 316 alloys are commonly used in fracture fixation devices. They are commonly hot- or cold-worked and solid solution–strengthened.
Titanium-Based Alloys
Titanium-based alloys currently are the alloys most commonly used for bioimplantation. Pure titanium (cP-Ti) and an alloy with aluminum and vanadium (Ti-6Al-4V) are the most common compositions for titanium in the United States.1,5
Titanium-based alloys are advantageous for several reasons. They have both high strength and fatigue resistance. Commercially pure titanium has a hexagonal, close-packed structure; various grades differ in their oxygen concentration. In small quantities, oxygen serves to solid-solution strengthen the alloy by interstitial placement of the atom. However, in excessive amounts, oxygen can weaker the material by decreasing the number of grain boundaries. This results in a much lower fatigue strength and surface ductility.1,5,8 Titanium-based alloys also have decreased stiffness when compared to stainless steel. The reduction in stiffness facilitates transfer of the stress at the bone-implant interface to the alloy; this minimizes bone resorption at the interface. Titanium-based alloys have higher fatigue strength when compared with stainless steel. However, titanium alloys are vulnerable to any surface flaws. Any scratch or notch can rapidly accelerate the fatigue failure process. Titanium, in its pure form, is generally weaker than stainless steel, but it can be cold-worked to increase its strength.1,2 Titanium alloys also lack any known immunogenicity, an important advantage for any foreign body implant.
Surface Structure and Modifications of Alloys
As discussed previously, any surface component that prevents crack formation will decrease an alloy’s sensitivity to fatigue. Implant alloys typically use an oxide film for their surfaces. These oxide films are considered passive films because they are the result of oxidation of the outermost metal atoms on the surface of the alloy.1
Surface modification is used to increase local strength and hardening of implants. Two types of surface modification include ion implantation and vapor deposition.1,5 Ion implantation, the direct implantation of gas phase ions into the alloy, involves the acceleration of ions toward the surface of the alloy. The ions penetrate and increase the number and type of subsurface defects and dislocations, which leads to an increase in the durability of the metal surface and a reduction in its susceptibility to corrosion.1,9
Finally, nitriding is a process that modifies the surface of a material by a chemical reaction with nitrogen, which places nitrides on the surface. A portion of the surface of stainless steel or titanium can undergo nitriding by causing the surface to react with either gaseous ammonia or molten potassium cyanate.1,5 The result is a great increase in surface hardness of the alloy.
Ceramics
In contrast to metals, ceramics have chemical bonds that are predominantly ionic, with a densely packed array of oppositely charged atoms (Fig. 20-8). These atoms have limited mobility because of the interaction of charges of nearby atoms. This charge interaction results in a stiff material with low ductility and no plasticity. Ceramics are composed of crystals oriented randomly in a dense framework that consists of metallic oxides. They may have inorganic chain molecules, such as silicon dioxide in a glass phase. Traditional ceramic materials often have impurities and internal microporous inclusions that limit their strength to less than the theoretical maximum. Newer ceramics are synthesized with chemically pure materials with high densities or as composites with greatly increased strength.10–12
An advantage of oxide ceramics is their wear reduction compared to that of alloys.1,10 Metals and alloys have a protective oxide film that can be peeled off by adherence to opposing surface polymers.1,10 This causes local ion release from the alloy. This loss and reformation of the oxide film is a repetitive process that can accelerate degradation of the surface of the alloy implant. Oxide ceramics do not have a passive oxide film and may, as a result, have less long-term breakdown.
Synthetic Polymers
Synthetic polymer production is a rapidly expanding field of implant technology. Polymers, commonly known as plastics, typically are very large molecules made from a large number of individual subunits called monomers. Polymers are chemical compounds that are formed by combining these smaller, repeating structural units. The subunits repeat in various patterns, following principles similar to those of molecular biology. The covalent bonds in polymers have a fixed length. The complex folding of polymers is created by weak hydrogen bond cross-links that permit unfolding and elongation. The two most commonly used polymers are polymethylmethacrylate (PMMA) and ultra-high molecular weight polyethylene (UHMWPE).1
Composite materials are a combination of a filler and matrix. Traditionally, the filler is glass or carbon fibers, whereas the matrix is epoxy, carbon, UHMWPE, PMMA, or a variety of other materials. The fibers can be particulate or relatively large and stiff, in which case they are termed whiskers. Composites with whiskers have high tensile strength but can be brittle. Fiber orientation in relation to the direction of loading is important. A complex variety of stress responses can be obtained in polymer matrix composites, making these materials anisotropic. Biologic materials such as bone, ligament, and tendon also are composites with anisotropy. An example of a composite used in spine surgery is the carbon fiber cage for interbody fusion, which is composed of long-fiber carbon and Ultrapek (polyether ketone; BASF Aktiengesellschaft, Germany).13
Bone Morphogenetic Protein
The use of growth factors such as BMPs is showing great promise in spinal surgery and has been used successfully in spine fusion and fracture healing.14 Several animal models have demonstrated that BMP-containing allograft or synthetic carrier medium is as effective as or superior to autograft bone in promoting spinal fusion.15 Burkus et al. have illustrated that in ventral lumbar fusions, allograft cortical bone with rhBMP had equivalent fusion rates as autogenous bone graft without the associated graft site morbidity.16
Recombinant human bone morphogenetic protein type 2 (rhBMP-2) has been demonstrated to be safe and effective in posterior lumbar interbody fusion procedures when used as an absorbable collagen sponge carrier as an alternative to iliac crest bone graft.17 The efficacy of rhBMP-2 in augmenting fusion also has been shown when used in non-instrumented posterior lumbar decompressive surgery and leads to satisfactory outcomes, specifically improved pain relief, function, and bone formation, in elderly patients without the use of instrumentation.18 In addition to lumbar surgery, a prospective nonrandomized study in patients undergoing anterior cervical discectomy and fusion has demonstrated that those performed with BMP allograft are as effective as iliac bone graft in terms of patient outcomes and fusion rates.19
Biocompatibility
In total joint replacement, wear debris accumulates as a function of the force across the joint, the relative displacement of the articular surfaces, and a variety of wear mechanisms, including abrasion, corrosion, fretting (micromotion), and third-body wear resulting from wear debris between the articular surfaces. Wear debris also can cause adverse local responses to the implant, such as osteolysis and regional lymphadenopathy. These phenomena are of increasing interest to neurosurgeons, because articulating artificial discs have become more widely used as an alternative to spinal fusion.20–22
Metal allergy is widely prevalent and well recognized, but is poorly understood. Metal ions alone will not stimulate the immune system. When linked with proteins, metals such as cobalt, chromium, and especially nickel are immunogenic. The characteristic immune response to metals is delayed hypersensitivity. This has been proposed as the cause of premature loosening in total hip arthroplasties. Delayed development of sensitivity after prolonged exposure to a metal implant has been well documented, using the leukocyte migration inhibition test.23 The clinical significance of metal allergy in spinal surgery is unknown, but these data suggest that patients reporting skin sensitivity to metal should be considered for titanium implants rather than stainless steel before elective spinal surgery.
The mechanical strength immediately after instrumentation is determined by the worst case of device-graft subsidence; after instrumentation, bone will adapt itself to the changed loading conditions and therefore reduce the risk of subsidence.24 Knoller et al. demonstrated a relationship between the stability of a spinal instrumentation and bone mineral density and a significant influence of bone mineral density on range of motion.25
Osteolysis, or periprosthetic bone loss, may occur at the site of an implant. Structural remodeling of surrounding bone occurs in response to stress shielding. This bone destruction can lead to loosening and possible failure of the implant. Factors that are thought to play a role in osteolysis include the formation of particulate debris and loosening, or motion, of the implant.6 Once the particles are generated, macrophages proliferate and attack the periprosthetic space. This leads to activation of an inflammatory cascade and the induction of osteoclastic pathways.
Highsmith J.M., Tumialan L.M., Rodts G.E.Jr. Flexible rods and the case for dynamic stabilization. Neurosurg Focus. 2007;22(1):E11.
Merritt K., Brown S.A. Biological effects of corrosion products from metals (195-206). In: Fraker A.G., Griffin C.D., editors. Corrosion and degradation of implant materials. ASTM STP 859. Philadelphia: American Society for Testing and Materials, 1985.
Wang X., Dumas G.A. Evaluation of effects of selected factors on inter-vertebral fusion-a simulation study. Med Eng Phys. 2005;27(3):197-207.
White A., Panjabi M. Clinical biomechanics of the spine. Philadelphia: Lippincott-Raven; 1990. pp 86–87
1. Bradley R.J., Chaoi E.Y.S., Friedman J. Biomechanics and biomaterials. In: Dee R., Hurst L., Gruber M., Kottmaier S., editors. Principles and practice of orthopaedics. ed 2. New York: McGraw-Hill; 1997:151-174.
2. Friedman D.W., Orland P.J., Greco R.S. Biomaterials: an historical perspective. In: Greco R.S., editor. Implantation biology: the host response and biomedical devices. Boca Raton, FL: CRC Press; 1994:1-12.
3. Meij B.P., Suwankong N., Van der Veen A.J., Hazewinkel H.A. Biomechanical flexion-extension forces in normal canine lumbosacral cadaver specimens before and after dorsal laminectomy-discectomy and pedicle screw-rod fixation. Vet Surg. 2007;36(8):742-751.
4. Prakash, Prabhu L.V., Saralaya V.V., et al. Vertebral body integrity: a review of various anatomical factors involved in the lumbar region. Osteoporos Int. 2007;18(7):891-903.
5. Gilbert J.L., Callaghan J.J., Rosenberg A.G., Rubash H.E., editors. The adult hip. Philadelphia: Lippincott-Raven Publishers, 1998. Metalspp 123–134
6. Highsmith J.M., Tumialan L.M., Rodts G.E.Jr. Flexible rods and the case for dynamic stabilization. Neurosurg Focus. 2007;22(1):E11.
7. Ahn Y.H., Chen W.M., Lee K.Y., et al. Comparison of the load-sharing characteristics between pedicle-based dynamic and rigid rod devices. Biomed Mater. 2008;3(4):44101.
8. Rae T. The toxicity of metals used in orthopaedic prosthesis. An experimental study using cultured human synovial fibroblasts. J Bone Joint Surg [Br]. 1981;63:435.
9. Reinscb W.A. Terminology for titanium microstructure. In: Titanium and titanium alloys: source book. Metals Park, OH: American Society for Metals; 1982:p 47.
10. Cooke F.W. Ceramics in orthopedic surgery. Clin Orthop. 1992;276:135.
11. Park J.B., Lakes R.S. Biomaterials: an introduction, ed 2. New York: Plenum Press; 1992. pp 117–140
12. White A., Panjabi M. Clinical biomechanics of the spine. Philadelphia: Lippincott-Raven; 1990. pp 86–87
13. Albrektsson T., Branemark P.I., Hansson H.A., Lindstrom J. Osteointegrated titanium implants. Acta Orthop Scand. 1981;52:155.
14. Lane J.M. Bone morphogenic protein science and studies. J Orthop Trauma. 2005;19(Suppl 10):S17-S22.
15. Zlotolow D.A., Vaccaro A.R., Salamon A.L., Albert T.J. The role of human bone morphogenetic proteins in spinal fusion. J Am Acad Orthop Surg. 2000;8(1):3-9.
16. Burkus K., Sandhu H., Gornet M., Longley M. Use of RHBMP-2 in combination with structural cortical allografts: clinical and radiographic outcomes in anterior lumbar spinal surgery. Bone Joint Surg [Am]. 2005;87(6):1205-1212.
17. Dickerman R.D., Reynolds A., Tackett J., et al. Bone morphogenic protein. J Neurosurg Spine. 2008;9(4):401.
18. Geibel P.T., Boyd D.L., Slabisak V. The use of recombinant human bone morphogenic protein in posterior interbody fusions of the lumbar spine: a clinical series. J Spinal Disord Tech. 2009;22(5):315-320.
19. Hamilton D.K., Jones-Quaidoo S.M., Sansur C., et al. Outcomes of bone morphogenetic protein-2 in mature adults: posterolateral non-instrument-assisted lumbar decompression and fusion. Surg Neurol. 2008;69(5):457-461.
20. Hedinan T., Kostuik J., Fernie G., Hellier W. Design of an intervertebral disc prosthesis. Spine. 1991;16:S256-S260.
21. Blumenthal S., McAfee P.C., Guyer R.D., et al. A prospective, randomized, multicenter Food and Drug Administration investigational device exemptions study of lumbar total disc replacement with the CHARITE artificial disc versus lumbar fusion: part I: evaluation of clinical outcomes. Spine. 2005;30(14):1565-1575.
22. Moreno P., Boulot J. [Comparative study of short-term results between total artificial disc prosthesis and anterior lumbar interbody fusion. Rev Chir Orthop Reparatrice Appar Mot. 2008;94(3):282-288.
23. Merritt K., Brown S.A. Biological effects of corrosion products from metals. In: Fraker A.G., Griffin C.D., editors. Corrosion and degradation of implant materials. ASTM STP 859. Philadelphia: American Society for Testing and Materials; 1985:195-206.
24. Wang X., Dumas G.A. Evaluation of effects of selected factors on inter-vertebral fusion-a simulation study. Med Eng Phys. 2005;27(3):197-207.
25. Knoller S.M., Meyer G., Eckhardt C., et al. Range of motion in reconstruction situations following corpectomy in the lumbar spine: a question of bone mineral density? Spine. 2005;30(9):E229-E235.