Chapter 93 Outdoor Clothing for the Wilderness Professional
For online-only figures, please go to www.expertconsult.com
There are several factors to keep in mind when choosing the appropriate clothing. These include the weather, influenced by geographic location and season; and the specifics of the activity, such as aerobic or high-exertion sports compared with sedentary tasks. One must also consider the length of the outing. For example, an activity in a remote locale lasting a long time will require different clothing than a short outing close to an urban environment. In the wilderness setting, the clothing one wears is not just for personal adornment or comfort—it may be a lifesaving feature (Box 93-1).
BOX 93-1 Considerations for Clothing Choice
These considerations apply to any length excursion, from day trip to multiweek expedition.
This chapter discusses the various fabrics and fibers used in outdoor clothing and illustrates an adaptive strategy for picking the appropriate garment type and accessories for use in various environments (Figure 93-1).
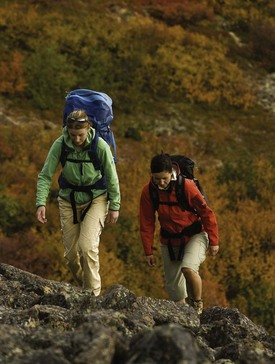
FIGURE 93-1 Alaska hiking in Arc’teryx clothing and packs.
(Copyright 2008 Arc’teryx. Courtesy Brian Goldstone. http://www.arcteryx.com.)
Fabrics and Fibers
Natural Fibers
Wool and merino wool are excellent insulating fabrics (Figure 93-2, online). The core of the wool fiber absorbs moisture and redistributes it to the fabric surface, where evaporation occurs. This moderate affinity for absorbing moisture is countered by excellent regain—the fabric retains warmth and does not feel cool or wet when damp. Wool feels wet when saturated. Traditional wool can be highly irritating to the skin. Wool fibers have barbs in the epicuticle, or outer layer of the fiber. Merino wool is a finer fiber with fewer barbs in the epicuticle. Ultrafine merino wool fibers are 17.5 µm in diameter, allowing for lightweight fabrics and exceptionally tight weaves. (For comparison, a human hair is 60 µm in diameter.) Merino wool is machine washable with minimal shrinkage and is highly elastic. It retains its shape well with repeated wearing and washing. The antibacterial properties of wool contribute to decreased body odor retention—a very desirable quality when faced with multiple days of wear. The bacteria that metabolize sweat do not flourish; therefore less odor-producing metabolites are present.
Wool, including merino wool, is spun from the fleece of sheep. Alpaca and llamas are camelids, originally from South America (Figure 93-3). Cashmere is spun from the undercoats of cashmere goats. Although technically not wool, these wool-like fibers share similar properties with Merino wool.
Down
Down is the fluffy undercoating that keeps geese, ducks, and other waterfowl warm (Figure 93-4). It consists of clusters of filaments growing from a central quill point. Land fowl do not produce down. Goose down is superior to duck down in its loft and therefore ability to insulate. Down is an excellent insulator when dry. Unfortunately, the low moisture regain and hydrophilic nature of down make it almost useless when wet. The insulative value of down is measured in fill power. Each company uses a slightly different measurement, making across-the-board comparisons difficult. Generally, the higher the fill power, the greater the insulative value. Fill power is the volume that a specific weight of down occupies. In other words, the number of cubic inches displaced by a given ounce of down (in3/oz) is the fill power.
Synthetic Fibers
Blends
Manufacturers blend fiber types to use the benefits of each fabric. For example, spandex may be blended with the primary fiber, such as wool or cotton, to improve stretch and retention of shape. Wool may be blended with polyester to improve durability and fit (Tables 93-1 and 93-2).
Down | Synthetic | |
---|---|---|
Compressibility | Excellent | Good |
Insulative quality when wet | Poor | Good |
Weight | Lighter per volume | Heavier than down |
Durability | Will last longer if cared for properly | Will eventually break down even with ideal care |
Care | Requires careful laundering | No special product required |
Warmth | Greater warmth-to-weight ratio | |
Allergenic properties | Possible | None |
Expense | High | Moderate |
Drying time | Slow | Fast |
Waterproof/Breathable Fabrics
Laminates
Laminate fabrics are designed by bonding a waterproof/breathable membrane to the underside of the garment’s exterior. They are commonly bound to nylon. If there are only two layers, the fabric is designated “two-ply.” The laminate may be sandwiched between two layers, thus creating a three-ply material, which is more durable but heavier than two ply. W. L. Gore and Associates produced the first waterproof/breathable membrane—Gore-Tex. This trade name is commonly, and incorrectly, used to refer to the entire category of laminate clothing (Figure 93-5). Although many manufacturers and laminate types now exist, the basis of laminate technology is the membrane. The membrane is formed of stretched or expanded polytetrafluoroethylene (ePTFE). The process of expanding the PTFE introduces microtears or holes in the laminate. These openings are small enough to allow water vapor of perspiration to escape (breathability), while not allowing water droplets to enter from the environment (water resistance). The pores of the ePTFE are 20,000 times smaller than the smallest raindrop, yet large enough to allow water vapor to pass to the outside. Water can only penetrate ePTFE if it is applied with a great deal of force or if the surface of the ePTFE is contaminated or soiled, leading to leakage. Two of the predominant manufacturers, Gore and eVent, use different methods to address soilage. Gore applies a microthin layer of polyurethane to the laminate. It is designed to be porous and not affect breathability of the fabric. eVent uses a proprietary method employing integration of a substance into the laminate itself. By preventing soilage, the waterproof and breathable properties of the fabric are sustained.
Soft-Shell Fabrics
Soft-shell fabrics are the most newly developed fabrics in the outdoor clothing industry. This fabric type excels in breathability and flexibility yet still demonstrates moderate water resistance. Soft-shell fabrics have a tightly woven outer layer and an inner lining of varying insulative quality and may additionally employ a windproof or highly water-resistant laminate (Figure 93-6, online). They combine the properties of both an insulating middle layer with a protective outer layer. Soft-shell garments are highly effective for both temperature and moisture management in environments where rain is unlikely. They are moderately water resistant due to the tightly woven exterior surface and DWR finish. These garments excel when used during highly aerobic activities and in conditions where rain is not a concern. Soft-shell garments may function as both an insulating (middle) and outer (protective) layer.
Durable Water-Repellent Finish
A DWR finish is applied to all waterproof/breathable fabrics after the garment is completed. It does not change breathability of the fabric but enhances water resistance by causing water to bead up and roll off the garment’s exterior. The finish bonds to the fibers and does not fill the interstitial spaces of the fabric. An ideal DWR finish forms a dense chemical buffer on the outer surface of the garment. Microscopically, the finish forms an upright, spiky, and brush-like texture. Water thereby has a high contact angle with the finish, forming a spherical droplet. Were the contact angle to be low, water droplets would flatten into a more dome-like shape. This would allow the water to cling to the surface of the fabric and eventually seep in (Figure 93-7).
Layering
Dressing in layers enhances one’s ability to adapt to a changing environment. Each layer should maximize the properties of the fabric from which it is made. Layering allows for addition and subtraction of clothing as needed, adjusting for changes in body temperature and metabolic output, resulting in more efficient maximization of metabolic heat and enhancement of energy conservation. Adjustment of layers in response to changes in the environmental or travel conditions can prevent sweating and overheating, while preventing loss of heat that might lead to undesired cooling. In anticipation of increased body heat and sweating when traveling uphill, layers can be preemptively removed and zippers unzipped to enhance ventilation. Clothing that becomes saturated in sweat is not only uncomfortable, but loses its insulative properties as the fibers become soaked with moisture. This is clearly important in a cold environment, where loss of insulation or long drying times may lead to hypothermia. Removing layers in response to increased work also serves to conserve energy and moisture. In contrast to removing layers to prevent sweating, adding clothing layers as the workload decreases or the environment cools allows heat to be trapped in the insulative layers. The simple actions of managing a personal layering system conserve valuable energy for outdoor endeavors (Figure 93-8, online).
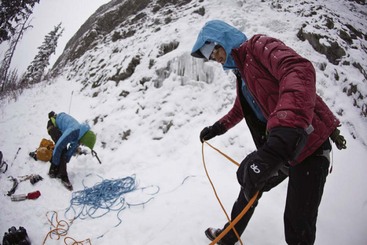
FIGURE 93-8 Sarah Hueniken keeping warm layered up in Outdoor Research clothing between climbs.
(Copyright 2009, Ryan Creary, Outdoor Research Marketing. http://www.outdoorresearch.com.)
An efficient layering system allows rapid response to changing environmental conditions. It is easier to replace a single garment that has become soiled or saturated than to replace an entire suit of clothing. Through layering, it becomes possible to not only pack fewer garments, but still be more comfortable across a wider range of environmental conditions and activity levels. When packing for any wilderness excursion, the unexpected needs to be considered, such as precipitation in the form of rain or snow, a sudden change in temperature, or the unexpected night out. When dressing in layers, fit is very important. The base layer should be snug but not confining. The middle layer should fit over the base layer comfortably. The outer layer needs to be large enough to fit over both base and middle layers without compressing. Compressing the middle layer reduces its insulative properties. Harness or pack straps should not rub or chafe on any seam or fold of fabric. Testing the fit, comfort, and effectiveness of the layering system before venturing into the wilderness will help prevent not only the discomfort of poor-fitting layers, but ensure that the purpose of the layering system is fulfilled—keeping one warm and conserving energy (Box 93-2).
BOX 93-2 Insulating Value of Clothing
Approximate clo Range | Garment Example | |
---|---|---|
Base | 0.15-0.3 | Silk weight, cotton T-shirt |
Lightweight | 0.30-0.50 | Polartec 100, Patagonia R1 |
Midweight | 0.75-0.85 | Polartec 200, MontBell Thermawrap parka |
Heavyweight | 0.90-0.11 | Polartec 300, Patagonia Polarguard Delta pullover |
Expedition | 1.40 and greater | Patagonia down pullover and most high-loft insulation |
Base Layer
The base layer is next to the skin. It may be as sparse as briefs and a sports bra or as extensive as full-coverage long underwear. The primary function of the base layer is to regulate body temperature by retaining heat and transferring moisture away from skin (Figure 93-9). Moisture management is accomplished by the wicking properties of the fabric. Moisture is drawn away from the skin surface by the hydrophilic properties of the fiber. The hydrophobic properties of the fiber transfer, or “wick,” moisture to the outer surface to be evaporated. This layer must fit without binding seams or wrinkles, allowing for ease of movement without restrictions. Usual base-layer fabrics are supple and flex easily with motion. Most good insulative base-layer garments are made of polyester, merino wool, silk, or a blend of fiber types. Poor base-layer garments are made of fabrics that lose their insulative properties when wet, such as cotton.
Base layers are available in ultralight, light-, mid-, and expedition weights. The weight of a garment is a relative measure and varies among manufacturers (see Box 93-2). The choice depends on the activity and environmental conditions. In mild and moderate conditions, a lightweight or midweight layer is appropriate. In conditions of extreme cold, a heavier base layer that maximizes heat retention is preferred. Base layers may have zippers for ventilation. If aerobic, vigorous, and heat-producing activity is likely, consider choosing a top with a zipped neck. This allows increased air movement around the neck and can be rapidly closed to restore protection. Bottom layers are available with zippers or overlapping flaps of fabric to facilitate heat and moisture elimination. With a properly fit system, significantly less skin is exposed to the cold, and harnesses do not need to be removed. One-piece base layers cover both top and bottom with a single garment. Most are designed with long zippers to allow ventilation and elimination. Generally these garments are suited only for extreme cold, where even the chance of exposure through a waistline gap would be dangerous.
Outer Layer
Pants should be loose enough to permit unrestricted movement and have no excess fabric to get caught or tangled in straps, crampons, or brush. Full-length zippers permit removing pants without taking off boots. Hand pockets are rare in technical garments; however, if they are present, they should not rub or chafe. Accessory pockets on the thighs should fasten closed and have minimal bulk. The waistband optimally has little bulk and should not interfere with backpack hip belts or harnesses (Figure 93-10, online). Bibs are another choice. They keep the chest and torso warmer and protect against wind and snow. As with the base and middle layers, many garments have a full fly that zips through to the back of the garment.
Accessories
Headgear
Adequate headgear is necessary regardless of the climate, whether to protect from the environment or prevent heat loss through the scalp. Brimmed hats and caps shade the face, ears, and neck from the sun, which is necessary in sunny environments, especially when there are reflective sources such as water or snow. Hats for sun protection need to have a broad enough brim to shade the face, ears, and neck. Ball caps, cowboy hats, and fishing “bucket hats” are common. In mild conditions, thin skull caps and bandanas may be fashioned into headgear. Insulating headgear is manufactured out of most fabrics. As with all other layers, the anticipated environment, activities, and length of excursion need to be considered. Knit hats are made from both wool and/or synthetic yarns and may vary in thickness from microweight to heavy weight. Hats may be lined with a wind-resistant or insulating layer or made exclusively from fleece fabrics. Hats need to fit snugly enough to keep from shifting and blowing off, but not so snugly as to constrict and be uncomfortable. Earflaps and tassels must not interfere with helmet fit; the hat needs to fit comfortably under the hood of an outer layer (Figure 93-11).
Neckwear
Scarves, neck gaiters, and balaclavas are common forms of neckwear. Scarves may range from a cotton bandana to a long woven or knit wrap. Long scarves are useful for full neck, face, and head protection. However, they may be cumbersome and are not appropriate if they may get caught in hardware. Neck gaiters are tubes of fleece, wool, or other knit fabric designed to pull over the head and encircle the neck (Figure 93-12). Neck gaiters retain heat and protect the neck from sun, wind, and cold. Similar to headgear, they need to fit well, not be too snug, and allow for helmets and other protective gear to be worn comfortably. The balaclava is an integrated head and neck layer, perhaps best described as a very long hat with an opening for the face (Figure 93-13). It is a versatile accessory and when pulled down around the neck has no openings around the neck or scalp to allow escape of warmth or entry of cold air. Hats may have an integrated skirting or tails to cover the neck and ensure that there is still adequate airflow.
Handwear
Gloves and mittens provide physical protection from cuts and scrapes and environmental protection from frostbite and sunburn. Handwear ranges from thin cotton, wool, or synthetic “liner gloves” to abrasion-resistant, waterproof, and insulated gloves or mittens for environmental extremes. Gloves with separated fingers allow for increased dexterity but are not as warm as mittens. Mittens separate only the thumb, providing maximal warmth (Figure 93-14).
Liner gloves are thin, permitting maximal dexterity and some protection from the environment. In extreme cold, this thin layer may protect against frostbite during brief exposures. If the liner snags or tears, it should be repaired or replaced. Liners are commonly worn under heavier gloves or mittens. This follows the principles of layering but also provides a measure of protection if the outer layer must be removed for tasks requiring more dexterity (Figure 93-15, online).
Gloves vary tremendously. Hybrids of synthetic and natural materials are used, such as a soft-shell or laminate body and a leather palm (Figure 93-16). Fleece gloves provide excellent insulation and may have a wind-stopper laminate. Hard-shell, laminate gloves are available both as shells to be worn over other glove layers and with integrated insulation. Neoprene gloves are manufactured for marine and extremely wet conditions. It is common to have multiple pairs of gloves on any trip, although an efficient combination of glove and mitten layers may minimize number of pairs and maximize protection.
Footwear
Boots and shoes have become very specialized. Professional fitting is ideal when acquiring footwear. A well-fit boot or shoe has no heel rise and adequate room at the toes to move or wiggle them. The foot does not slide forward, and there are no pressure points or painful areas (Figure 93-17, online). Some people require custom orthotics or boot liners to achieve a good fit. The sole is constructed of a rubberized polymer with a tread pattern. The tread maximizes traction on uneven surfaces. Trail shoes are designed with a flexible sole (Figure 93-18, online). Hiking and mountaineering boots may have a metal shank in the sole to provide additional stability on uneven surfaces, with full-shank boots being the most stable (Figure 93-19).
Footwear is constructed from a wide range of materials, and most are available with a waterproof breathable membrane. Fabric or mesh construction is the norm for trail shoes or light hiking boots. Leather is commonly sewn over points of stress or common areas for abrasion. More substantial boots are designed with more leather or a synthetic analog to increase stability and durability. Mountaineering boots are usually constructed of plastic or a semirigid synthetic (Figure 93-20). Boots designed for extreme cold and high altitude have removable and, in many cases, custom-molded boot liners. Double boots are designed to be maximally insulating and still allow for dexterity while walking and climbing (Figure 93-21).
Gaiters and overboots are designed to protect and insulate footwear. Constructed of abrasion-resistant nylon with or without a waterproof/breathable laminate, gaiters are tube-like constructions that either pull over or zip around the lower leg (Figure 93-22). They keep dirt, stones, mud, and snow out of shoes and boots. Supergaiters cover the entire boot, with a rubber rand that covers the boot rand. In addition to the protective qualities of standard gaiters, many have a quilted lining and provide additional thermal insulation for the feet. Supergaiters leave the boot sole free so that traction is maintained and crampons do not need to be refit. Overboots cover the entire boot, providing further insulation from the cold ground. Generally, overboots have a fabric sole and do not provide any traction. Crampons need to be fit to accommodate overboots (Table 93-3).
Shoe Type | Common Use | Advantages and Disadvantages |
---|---|---|
Sandals | Water sports | Well ventilated and quick drying |
Provides protection to the sole of the foot | ||
Does not protect the toes or top of the foot | ||
Running shoes | Trail running | Good underfoot support and traction |
Lightweight and ventilated | ||
Poor ankle support | ||
Rock shoes | Rock climbing | Sticky rubber soles for traction on vertical surfaces |
Specialized sport shoe, not practical for other uses | ||
Water shoes | Kayaking, boating | Neoprene shoes for insulation in the water |
Rubber soles for traction on wet surfaces | ||
Little use outside the sport | ||
Approach shoes | Walking, easy hiking, approach to more strenuous climbs | Lightweight with adequate traction |
Not designed for strenuous hikes or unstable ground | ||
Hiking boots | Hiking, backpacking | Extensive range of design and materials from lightweight material to heavy leather |
Full and half shank for stability | ||
Excellent traction | ||
Mountaineering boots | Mountaineering, ice climbing | Double or single boots |
Crampon compatible | ||
Well insulating | ||
Heavy and not suitable for hiking | ||
Pac boots, Sorels | Insulated, water-resistant winter boots | Well insulated and water resistant |
Good for activities that do not require traction or maximal support (e.g., after ski, shoveling snow) |
Care and Storage of Clothing
Special-Use Clothing
Sun Protection Clothing
Clothing manufacturers report an ultraviolet protection factor (UPF) determined by using one of several rating systems. For comparative value, a plain white T-shirt has a UPF value between 5 and 9, whereas a sun protection garment has a UPF of 30 or more (Table 93-4).
General Rating | UPF Rating | UV Light Blocked (%) |
---|---|---|
Good | 15-20 | 93.3-95.8 |
Very good | 25-35 | 95.9-97.4 |
Excellent | 40+ | Above 97.5 |
Sport-Specific Clothing
Sport-specific clothing is not necessarily better than general outdoor clothing. The basic principles of construction and fabric utilization are the same, but the clothing has design properties specific to the sport. For example, outer layers for mountaineering and ice climbing have less fabric around the waist or a much shorter torso rise to accommodate a harness. Gloves must both insulate and allow dexterity. Pockets are situated on the chest, and hand-warmer pockets are frequently eliminated. Kayaking jackets have tight-fitting or neoprene cuffs and waistbands to reduce water entry into the garment. Rock-climbing clothing is snug fitting to prevent fabric from catching in gear. Specialty rock shoes are required (Figure 93-23). Desert environments require increased sun and heat protection. Jungle and snake-ridden areas demand protective boots and snug-fitting ankle and wrist cuffs.
Climate-Specific Clothing
When preparing for any excursion, the expected environment is one of the principal factors determining clothing choice. Different clothing systems are needed for each environment, but the basic principles of thermoregulation and moisture management through layering always apply. In addition to anticipating climate and weather extremes, physical features of the environment and the activity to be pursued are important considerations. A hike or backpacking trip though an open forest, tundra, or grassland will not subject clothing to the type of damage made likely by bushwhacking and scrambling over rocks. For all climates, nylon and cotton-polyester blends offer the most abrasion-resistant fabrics. Fleece and any fabric with a loose weave will snag and tear. The need for a garment to tolerate abrasion must be balanced with the considerations for insulation (Table 93-5).
Hot
Fabrics and design of hot-weather clothing must be able to both protect from the sun and keep the wearer cool (Figure 93-24). Air needs to circulate freely across the skin, while the clothing shields from UVR. A fabric’s ability to protect from the sun is rated as either the ultraviolet protection factor (Australia) or the clothing protection factor (United Kingdom). The fabrics are tested with a spectrometer to measure the ability to block UVR. Not all fabrics receive UV protective ratings, but they still provide a degree of sun protection. Tightly woven fabrics are more protective than materials with a loose weave. Wet fabrics lose protective value, as do worn or abraded fabrics. Air circulation optimizes both convective and evaporative cooling. Strategically placed vents and mesh panels combined with a loose fit maximize ventilation. Many garments are designed to be “convertible,” with zip-off pant legs and easily rolled-up sleeves, offering the wearer maximum versatility for changing conditions (Figure 93-25, online).
Temperate
Lightweight, quick-drying nylon clothing provides protection from the sun and from abrasion caused by brambles and brush. Polyester-cotton blends are also highly abrasion resistant and dry relatively quickly. Long sleeves and pants may be necessary for cooler evenings or rainy conditions. A lightweight middle layer, such as fleece or a heavy shirt, coupled with gloves and hat, will stave off evening chill. Wind and water protection are accomplished with a lightweight outer layer. A jacket constructed of a waterproof/breathable laminate is most versatile. If extremely wet conditions are expected and the chance of perspiration is low, consider a coated nylon garment (Figure 93-26).
Cold
Daytime low temperatures that drop below freezing characterize cold climates. Layering systems must accommodate both the relative midday warmth and the potential for precipitation in the form of rain and snow (Figure 93-27, online). Clothing does not dry readily in these conditions. Efficient moisture management is imperative to maintain warmth as temperature drops. The base layer should accommodate the warmth of the day and not contribute to overheating. A light or midweight pair of long underwear is preferable over heavyweight garments. Insulating middle layers that can be easily shed or added are key to maintaining comfort. Careful consideration of the garment’s properties, such as the ability to vent through neck and leg zippers and ease of putting the garment on over boots, harnesses, or helmets, enhances efficiency of the layering system. The outer, protective layer must be both wind- and water-resistant.
Extreme Cold
Extreme cold characterizes the conditions encountered at high altitude, in glaciated terrain, or at extreme latitudes. With few exceptions, these climates are dry with precipitation in the form of snow. High-latitude coastlines and conditions that produce ice fog are the rare times that penetrating moisture is present. Wind is a large factor contributing to heat loss. Garment properties, such as draw cords and waist skirts, keep the wind from entering. All skin must be covered. Gloves, hats, and balaclavas and/or neck gaiters are necessary. Clothing must be easily layered and not constrictive so as not to lose loft. In these conditions, removing an outer layer to add insulation may not be possible. An insulating parka that fits over the outer shell solves this dilemma. This situation is commonly encountered when mountaineering. Heat generated by climbing is rapidly lost, necessitating the added insulation (Figure 93-28).
Adventure Medical Kits. http://www.adventuremedicalkits.com.
Any Mountain. http://www.anymountain.net/topNav/glossary.asp.
Arc’teryx. http://www.arcteryx.com.
Backpacker Magazine. http://backpackermagazine.com.
Buzz Off. http://www.buzzoff.com.
Cox SM, Fulsaas K. Clothing and equipment. In: Cox SM, Fulsaas K, editors. Mountaineering: The freedom of the hills. ed 7. Seattle: The Mountaineers Books; 2003:8-42.
Davenport GJ. Personal protection. In: Wilderness survival. Mechanicsburg, Pa: Stackpole; 1998:10-49.
Escape2co.com http://escape2co.uk/advice/outdoor_clothing_glossary.htm
Ex Officio. http://www.exofficio.com.
Ganci D. Desert dress and paraphernalia plan. In: Desert hiking. Berkeley, Calif: Wilderness Press; 1993:39-72.
Holmer I. Protective clothing in hot environments. Ind Health. 2006;44:404.
Lanza M. Clothing and gear. In: Winter hiking and camping. Seattle: The Mountaineers Books; 2003:27-62.
La Sportiva. http://www.sportiva.com.
Loutens W. Actual insulation of multilayer clothing. Scand J Work Environ Health. 1989;15:66.
NikWax. http://www.nikwax-usa.com.
Outdoor Research. http://www.outdoorresearch.com.
Patagonia. http://www.patagonia.com.
Polartec. http://www.polartec.com.
Sun Precautions. http://www.sunprecautions.com.
Townsend C. Clothing for the snow. In: Wilderness skiing and winter camping. Camden, Maine: Ragged Mountain Press; 1994:160-194.
Van Tilburg CS. Backcountry snowboarding. Seattle: The Mountaineers Books; 1998.
Van Tilburg CS. Equipment. In: Canyoneering: Beginning to advanced techniques. Seattle: The Mountaineers Books; 2000:33-35.
Western Mountaineering. http://www.westernmountaineering.com.